COVID has become the very black swan that hardly anyone could have predicted in their business development strategy. It has tested the strength of many companies and industries around the world. Everyone had to adapt to new realities, look for new strategies, not just development, but first survival.
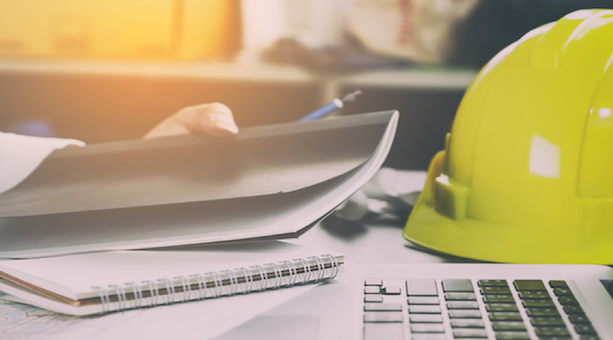
GlobalData holds a positive view on the outlook for the global construction industry following the historic collapse in activity in 2020 amid the severe disruption caused by restrictions imposed to contain the spread of COVID-19. The central forecast for growth in global output is 5.2%, which means that in real value terms, output in 2021 will be 2.5% higher than the 2019 level. Although recovering from the COVID-19 crisis, the global industry has borne a huge cost in terms of foregone revenue; compared to GlobalData’s pre-COVID-19 predictions for construction output value, the sum of output in 2020-2021 is close to US$1.1 trillion lower than it would otherwise have been.
source: Global Data
It is generally accepted that a crisis is a difficult but good time for development. According to Goldratt’s theory of constraints, any problem is the possibility of multiple growth. But in order to find points of growth, one should analyze what exactly the problem is, what impact and what it has, and then look for solutions to the problem. And of course, the one who is able to make decisions quickly and react to changes wins here.
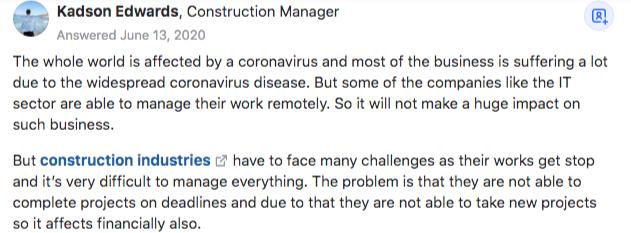
Source: Quora
Material Price Changes
One of the most visible and important impacts of the pandemic in the construction business has been the soaring material prices that have resulted from a global supply chain disruption affecting contractors.
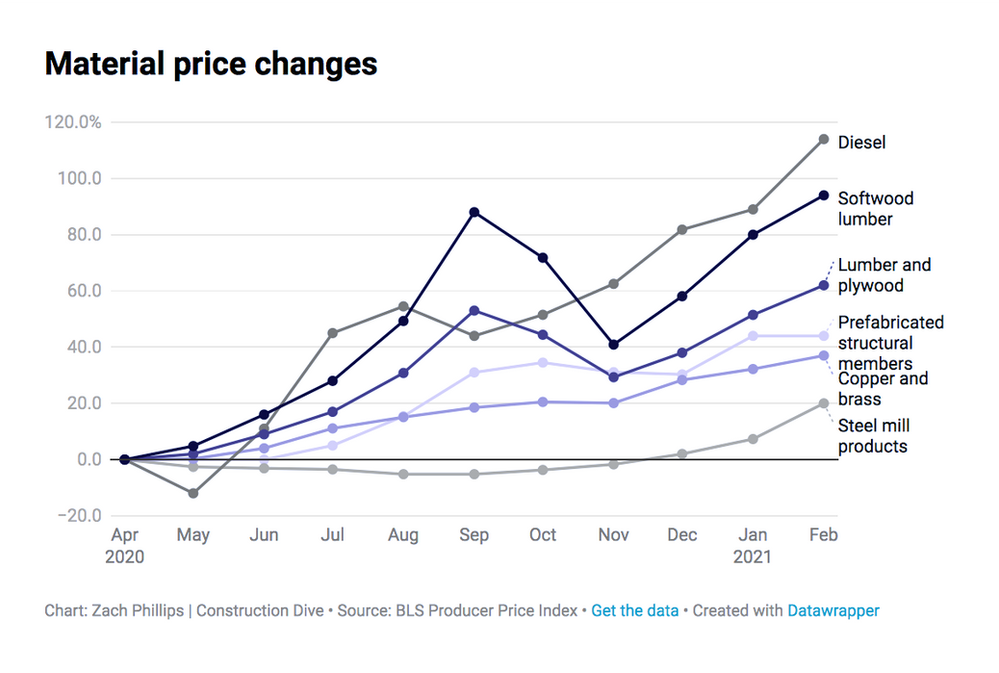
The Commercial Building Index, a quarterly economic indicator designed to measure the health of the construction industry, rose to 60 in the fourth quarter of 2020, well below 74 from 2020 but up from 57 in the third quarter. The index also shows that material prices are rising, with steel and other key products reporting multiple planned price increases in 2021. Trade contractors are reporting significant delays that are expected to last until the second quarter of 2021. They are also lagging behind their current projects and struggling to find labor.
For building materials such as aluminum, steel and timber, their overall base price is rising due to the newly introduced tariffs. This can increase the overall cost of construction and increase the profit margins for contractors. At the same time, we should take into account and edit points or add points to your contracts in order to leave space for maneuver when material costs change.
In addition to the short-term impact of the economic downturn on construction demand, the crisis is also expected to affect long-term supply and demand, leading to sustained changes in investment patterns.
Construction is usually much more volatile than the economy as a whole. The decline in economic activity leads to a decrease in demand for new commercial or industrial facilities, and the uncertainty further reduces the volume of investments. Loss of income and consumer distrust negatively affect demand for housing construction or renovation. And since the cost of buildings and infrastructure is closely related to GDP, the need for new construction is very sensitive to GDP growth, even in long-term models. For example, a four-year recession could significantly reduce the share of construction in GDP beyond the initial recession, even though the current crisis is not primarily related to real estate, as it was in 2008.
Material delays
It is conservatively estimated that nearly 30% of all US construction product imports come from China, but some US construction firms rely on China to produce up to 80% of their materials: because they are usually less expensive.
According to Joe Natarelli, national construction industry leader at Marcum, US builders look to China for everything from steel and stone to joinery and plumbing.
For commercial builders who rely on Chinese-made goods or materials, this could mean higher material costs and potentially slower project completion, said Construction Dive Richard Branch, chief economist at Dodge Data & Analytics.
“Almost every construction contract has a “time is of the essence” provision and a completion deadline. Absent a justifiable excuse, the consequences for failure to meet the completion deadline may include termination of the contract for default (usually accompanied by a demand on the performance bond surety to complete the work), payment of the obligee’s costs to supplement the principal’s labor force to mitigate delays, and/or the assessment of liquidated damages or actual delay damages for failure to timely complete the work. Significant project delays increase the surety’s risk of receiving both a performance bond claim from the obligee and payment bond claims from lower-tier vendors seeking progress payments and delay/impact costs.
The vast majority of construction contracts also contain provisions allocating the responsibility for the impacts of various delays. Provisions addressing delays that are caused by forces outside of either party’s control are typically referred to as “force majeure” clauses. Although their specific terms vary widely, there are two primary types of force majeure clauses: one type contains a non-exclusive list of examples of force majeure delays along with a “catch-all” provision containing language such as “or anything outside of either party’s control;” and the other type specifically spells out every calamity that will qualify as a force majeure delay. For those clauses containing a “catch-all” provision, a global pandemic very well may fall within the provisions of the clause. Clauses with ambiguous or narrower language may be subject to future litigation as to whether current circumstances meet the criteria.”
Source: Americcan Bar Association . Dealing With The Construction Impacts Of COVID-19
More eyes are on the growth and response of the construction industry than ever before.
A McKinsey report distinguished construction as one of the industries that has the potential to help both communities and economies recover following COVID-19. The steps construction companies take in the coming months could lead to the industry coming back stronger and more innovative. However, with any rapid transition, comes new risk.
The onset of COVID-19 introduced many new challenges to construction professionals. On top of a shortage of trained construction professionals that has been prevalent in the industry, companies are now facing restrictions on how many workers can be on a jobsite—all leading to a sudden increase in fatigue among workers. There is an increased focus on job safety training and physical fitness, as time off from the job during quarantine likely depleted some workers’ skills. Additionally, from mental distractions due to the stress of the pandemic to additional PPE requirements—there are many new obstacles workers in the construction industry are now facing.
For the construction industry, force majeure situations in business and at sites are common, but the pandemic has undoubtedly become a serious threat to everyone. Since March 2020, contractors have been forced to address shortcomings in their business practices and quickly implement new solutions to protect workers – not only from traditional workplace risks, but from a virus as small as 60 nanometers. Amid the subsequent closings, layoffs, and multiple American deaths, many firms are faced with some of the most difficult decisions ever made.
Despite the obvious challenges, this moment of testing has inspired positive change and digital transformation, which heralds long-term improvements in safety and productivity in the industry.